Implementar certas metodologias no dia a dia da sua operação é um passo fundamental para garantir melhores resultados. Ao gerir a manutenção com precisão, o PPCM maximiza a disponibilidade e a confiabilidade dos ativos, tornando‐se indispensável aos processos internos de qualquer empresa que busca eficiência e previsibilidade.
Empresas industriais e logísticas de alto desempenho têm algo em comum: todas mantêm processos bem estruturados e operam com base em dados confiáveis e atualizados.
Nesse cenário, o PPCM (Planejamento, Programação e Controle da Manutenção) se destaca como um pilar para maximizar a disponibilidade e a confiabilidade dos ativos, garantindo operações mais eficientes e ágeis.
A falta de um PPCM estruturado abre margem para paradas não planejadas, backlog de ordens de serviço, custos excessivos e perda de competitividade. Por isso, dominar essa metodologia é fundamental para escalar a produção com máxima produtividade e menor risco de falhas.
Continue a leitura e veja como aplicar o PPCM, na prática!
O que é PPCM?
O PPCM (Planejamento, Programação e Controle da Manutenção) é o conjunto de processos e métodos utilizados para otimizar as atividades de manutenção, garantindo que os ativos permaneçam disponíveis e confiáveis.
Essa metodologia ajuda a estruturar tudo o que precisa ser feito: desde a análise de falhas e levantamento de materiais, até o agendamento das equipes e o acompanhamento dos resultados, de forma proativa e evitando paradas não planejadas.
Ao manter mão de obra, peças e cronogramas alinhados com as demandas operacionais, o PPCM assegura que os recursos estejam disponíveis no momento certo, na quantidade adequada e com o custo mais competitivo.
No final das contas, trata-se de uma função crítica para fortalecer a estratégia industrial com maior consistência e previsibilidade, sobretudo em ambientes com alta variabilidade.
Quais são os objetivos principais do PPCM?
O PPCM tem como foco tornar a manutenção mais estratégica, garantindo que os equipamentos estejam disponíveis e operando com máxima eficiência, segurança e ao menor custo possível.
Ao estruturar o planejamento e a execução das manutenções, a metodologia contribui para alinhar os recursos técnicos e operacionais à realidade da planta industrial.
Um dos principais objetivos é reduzir falhas inesperadas, adotando uma abordagem preventiva e preditiva, em vez de reagir a paradas não programadas.
Isso assegura mais estabilidade nos processos produtivos e reduz prejuízos com interrupções imprevistas. Além disso, o PPCM busca otimizar o uso de mão de obra, peças e materiais, evitando desperdícios e melhorando o aproveitamento dos recursos disponíveis.
Outro benefício importante é o aumento da vida útil dos ativos. Com as intervenções realizadas no momento certo e da forma correta, os equipamentos mantêm sua performance por mais tempo, adiando a necessidade de substituição.
O PPCM também contribui para uma gestão de estoque mais eficiente, já que permite prever com mais precisão as peças e insumos necessários para cada manutenção, reduzindo tanto a falta quanto o excesso.
Por fim, ao garantir uma execução segura, econômica e padronizada das manutenções, o PPCM melhora a produtividade da equipe técnica, fortalece a confiabilidade dos ativos e eleva a capacidade de atendimento da operação, impactando diretamente a competitividade da empresa no mercado.
5 Passos para implementar o PPCM na empresa
A implementação do Planejamento, Programação e Controle da Manutenção exige uma estrutura organizada e uma atuação integrada entre áreas técnicas, operacionais e estratégicas.
Mais do que uma ferramenta, o PPCM é uma metodologia voltada a maximizar a disponibilidade e confiabilidade dos ativos por meio de uma gestão de manutenção eficaz. Para que funcione na prática, é necessário seguir algumas etapas fundamentais:
- Realize um diagnóstico dos processos atuais: mapeie os fluxos de informação, identifique gargalos e falhas de comunicação entre setores. Avalie também se existem problemas relacionados à baixa previsibilidade ou à execução das rotinas de manutenção.
- Defina o modelo de planejamento mais adequado: escolha entre abordagens como manutenção corretiva, preventiva, preditiva ou híbrida, considerando o tipo de operação, os equipamentos críticos e o nível de maturidade da empresa em gestão de ativos.
- Estruture uma equipe dedicada ao PPCM: monte um time técnico com experiência em manutenção industrial, engenharia de processos, logística e tecnologia da informação. A atuação conjunta com a engenharia de produto e a área de produção é indispensável.
- Implemente sistemas de apoio: utilize um sistema de gestão (como um ERP com módulo de manutenção ou um software específico de PCM) para centralizar informações sobre ordens de serviço, planejamento de paradas, controle de estoque e análise de falhas.
- Invista em capacitação e padronização: treine as equipes envolvidas e estabeleça rotinas operacionais claras, como abertura e fechamento de ordens de manutenção, registros de consumo de peças, inspeções periódicas e acompanhamento de indicadores de desempenho.
Quais as tecnologias e ferramentas para otimizar o PPCM?
A transformação digital da indústria tem ampliado as possibilidades de aplicação do Planejamento, Programação e Controle da Manutenção, tornando os processos mais automatizados, integrados e preditivos. Para que o PPCM funcione de forma estratégica, é essencial contar com ferramentas que conectem dados, equipes e ativos em tempo real.
Sistemas ERP com módulo de manutenção são a base para essa estrutura. Soluções como SAP, TOTVS ou Oracle JDE permitem planejar intervenções, controlar ordens de serviço e gerenciar recursos técnicos e materiais com maior precisão.
MRP e MRP II contribuem ao integrar necessidades de materiais à programação da manutenção. Essas ferramentas analisam listas técnicas, capacidades disponíveis e tempos de execução para otimizar o planejamento de recursos e evitar paradas desnecessárias.
APS (Advanced Planning and Scheduling) vai além do básico e permite simular diferentes cenários de execução. Com algoritmos de otimização, é possível equilibrar calendários, prioridades e disponibilidade de equipamentos, promovendo um uso mais eficiente dos ativos.
Soluções de BI e dashboards operacionais tornam o acompanhamento mais ágil. Ao visualizar KPIs de manutenção em tempo real, os gestores conseguem identificar desvios, agir preventivamente e ajustar o plano conforme necessário.
A integração com dispositivos IoT também tem ganhado espaço. Sensores conectados às máquinas fornecem dados atualizados sobre temperatura, vibração, consumo energético e ciclos de operação, gerando insights que alimentam o PPCM com informações precisas e em tempo real.
Outra ferramenta indispensável para modernizar o PPCM é o Aplicativo de Ordem de Serviço da uMov.me. Totalmente personalizável, ele permite que equipes de manutenção em campo recebam, executem e atualizem ordens diretamente pelo celular, com registros de fotos, assinaturas digitais, checklists técnicos e geolocalização.
As informações são sincronizadas em tempo real com o backoffice, permitindo à gestão acompanhar o andamento das manutenções, validar intervenções e tomar decisões baseadas em dados concretos. Com isso, o controle de falhas, tempo de execução e consumo de materiais se torna muito mais eficiente e transparente.
Principais indicadores de desempenho (KPIs) no PPCM
Monitorar o desempenho é essencial para garantir que o PPCM esteja entregando os resultados esperados. Alguns dos principais indicadores utilizados são:
- OTIF (On Time In Full): mede a eficácia nas entregas, avaliando se foram feitas no prazo e com a especificação correta. Reflete a confiabilidade do planejamento.
- OEE (Eficiência Global do Equipamento): considera disponibilidade, performance e qualidade, oferecendo uma visão completa da eficiência dos ativos.
- Giro de estoque: mostra com que frequência o estoque é renovado. Um giro alto costuma indicar bom planejamento de compras e uso adequado de materiais.
- Lead time de manutenção: corresponde ao tempo médio entre a identificação da falha e a conclusão da intervenção. Ajuda a validar a agilidade do processo e identificar gargalos.
- Aderência ao plano: compara o que foi executado com o que havia sido programado. Altos níveis de aderência revelam um PPCM bem estruturado e confiável.
Quais são os desafios do PPCM e como superá-los?
Mesmo com seus inúmeros benefícios, a adoção do Planejamento, Programação e Controle da Manutenção ainda enfrenta obstáculos relacionados a processos, pessoas e tecnologia. Para que o PPCM alcance seu potencial máximo, é preciso reconhecer essas barreiras e atuar de forma estruturada para superá-las.
Falta de dados confiáveis é um dos principais entraves. Sem informações precisas sobre o histórico de falhas, tempo médio entre reparos, consumo de peças e capacidade da equipe, a manutenção deixa de ser planejada e volta a depender de estimativas. A solução está em digitalizar os apontamentos de manutenção e integrar os sistemas de gestão, garantindo que os dados estejam atualizados e acessíveis.
Resistência à padronização também compromete a eficácia do PPCM. Processos manuais, registros inconsistentes e práticas informais dificultam a criação de um modelo estruturado. Nesse cenário, capacitar as equipes e promover uma cultura orientada por dados são ações fundamentais para consolidar rotinas confiáveis.
Integração entre setores é outro desafio. Quando manutenção, produção, compras e engenharia não se comunicam de forma fluida, as intervenções não ocorrem no momento ideal, impactando prazos e produtividade. A realização de reuniões periódicas de alinhamento e a definição de fluxos claros de comunicação ajudam a evitar conflitos de agenda e priorizações erradas.
Capacidade de resposta a variações operacionais também precisa ser considerada. Alterações no ritmo de produção, aumento inesperado na carga dos equipamentos ou falhas recorrentes exigem uma atuação ágil. Para isso, ferramentas que permitem simular cenários, replanejar ordens e reavaliar recursos disponíveis fazem toda a diferença.
Considerações sobre PPCM
O PPCM é uma metodologia essencial para empresas que desejam aumentar a confiabilidade dos seus ativos, reduzir paradas não programadas e melhorar a performance operacional.
Quando bem estruturado, ele permite prever necessidades de manutenção com maior precisão, otimizar o uso de recursos técnicos e financeiros e garantir mais estabilidade ao processo produtivo.
A adoção de tecnologias especializadas, integração entre áreas e monitoramento contínuo de indicadores fortalece o controle da manutenção e fornece uma base sólida para a tomada de decisão estratégica.
Se a sua empresa deseja fortalecer o PPCM e tornar a gestão da manutenção mais eficiente, vale a pena investir em ferramentas que automatizam processos, aumentam a visibilidade operacional e ajudam o time técnico a atuar com mais previsibilidade e precisão.
Deseja entender como otimizar o PPCM na sua empresa e garantir uma operação mais eficiente com o uso de aplicativos? Agende uma demonstração gratuita e descubra como as soluções e ferramentas adequadas podem ajudar o seu time!
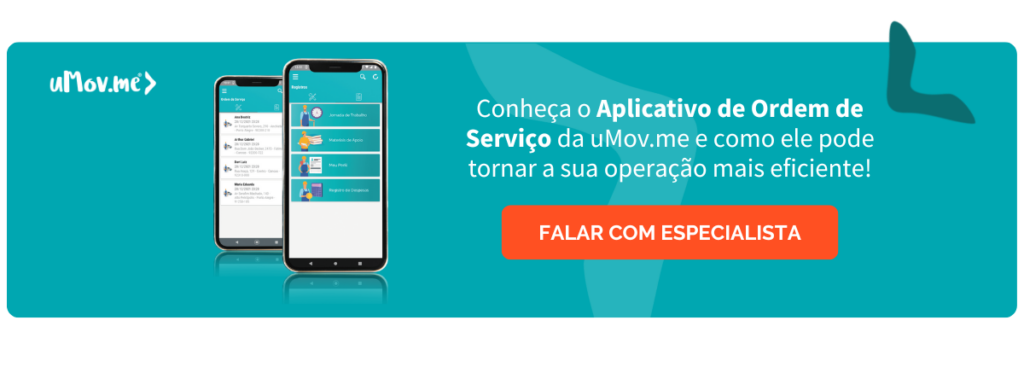